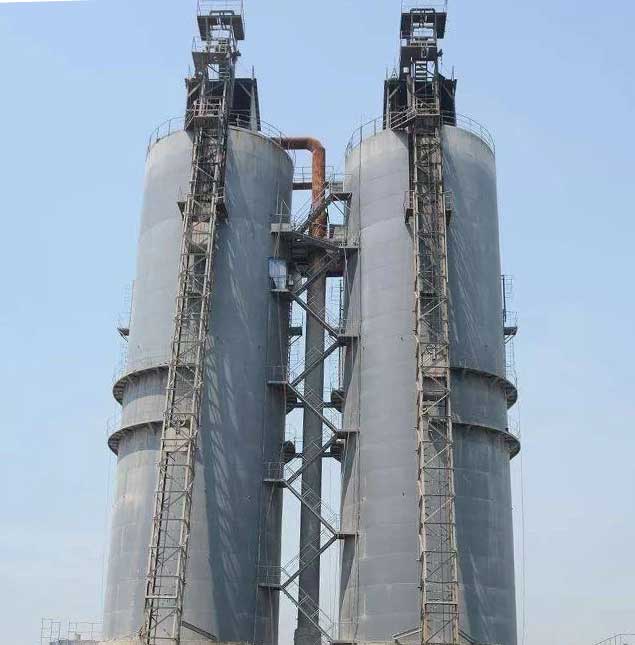
Five Crucial Cement Manufacturing Machines in a Cement Factory
- 0
Cement manufacturing is a complex, multi-step process that requires specialized machinery to transform raw materials into the final product. From crushing limestone to grinding clinker, each stage involves equipment that must operate efficiently and reliably. In this article, we’ll discuss five essential machines used in cement factories, including the coal grinding pulverizer mill system and screening machines, and how Cementl provides high-quality equipment for optimized production.
1. Crushers: The Starting Point of Cement Production
The cement production process begins with the extraction and crushing of raw materials like limestone, clay, and shale. Crushers reduce large rocks into smaller, manageable pieces, making subsequent grinding and processing more efficient.
Types of Crushers in Cement Plants:
- Jaw Crushers: For primary crushing with high capacity.
- Impact Crushers: For secondary crushing and material refinement.
- Hammer Crushers: Ideal for limestone due to their efficiency and simplicity.
Why Crushers Matter:
- Ensures uniform raw material size for efficient grinding.
- Reduces energy consumption during subsequent processes.
- Increases overall production efficiency.
Cementl offers robust, high-performance crushers designed for the demanding conditions of cement production.
2. Coal Grinding Pulverizer Mill System: Fueling the Kiln
Cement manufacturing relies heavily on high-temperature rotary kilns, which require a steady and consistent heat source. This is where the coal grinding pulverizer mill system comes into play.
How It Works:
Coal grinding mills pulverize coal into fine particles, which are then fed into the kiln for combustion. The finer the coal, the more efficient the combustion process, leading to improved kiln performance and lower fuel consumption.
Key Benefits:
- Efficient Combustion: Fine coal particles ensure complete combustion.
- Reduced Energy Consumption: Optimized grinding minimizes power use.
- Improved Kiln Stability: Consistent coal feed prevents kiln temperature fluctuations.
Cementl‘s advanced coal grinding pulverizer mill systems are engineered for efficiency and reliability, contributing to reduced energy costs and enhanced production consistency.
3. Rotary Kiln: The Heart of Clinker Production
The rotary kiln is central to cement manufacturing. It facilitates the chemical transformation of raw materials into clinker, the key ingredient of cement.
How the Rotary Kiln Works:
Raw materials, preheated in cyclones, enter the kiln, where temperatures reach up to 1450°C. The intense heat triggers chemical reactions, producing greyish-black nodules known as clinker.
Rotary Kiln Features:
- High Thermal Efficiency: Advanced insulation and refractory lining.
- Precise Temperature Control: Automated systems ensure optimal performance.
- Versatility: Can use alternative fuels like biomass and waste-derived materials.
Cementl manufactures durable rotary kilns with state-of-the-art control systems, ensuring maximum productivity and minimal environmental impact.
4. Vertical Roller Mill: Precision Grinding for Cement
Grinding clinker into cement requires specialized mills capable of producing fine, uniform particles. The vertical roller mill (VRM) has become the industry standard for this task.
VRM Advantages:
- Energy Efficiency: Consumes up to 30% less energy than ball mills.
- Consistent Product Quality: Adjustable settings for varying cement grades.
- Compact Design: Requires less space compared to traditional mills.
How It Works:
Clinker and additives like gypsum pass between rotating rollers and a grinding table, where they are ground into the desired fineness. The ground material is then pneumatically transported to a separator for particle size classification.
Cementl offers vertical roller mills equipped with advanced automation features to ensure high efficiency and product consistency.
5. Screening Machine: Ensuring Material Quality
The screening machine plays a vital role in cement manufacturing by sorting materials into specific sizes. From raw material preparation to final product packaging, screening machines ensure consistent quality and performance.
Applications of Screening Machines:
- Pre-Grinding: Separates oversized materials before entering the grinding mill.
- Post-Grinding: Ensures uniform cement particle size for consistent performance.
- Clinker Cooling: Screens cooled clinker to remove impurities.
Why Screening Matters:
- Improved Product Quality: Uniform particle size enhances cement performance.
- Reduced Equipment Wear: Prevents oversized particles from damaging downstream machinery.
- Operational Efficiency: Automates material classification for streamlined production.
Cementl‘s screening machines are designed for high throughput, minimal maintenance, and maximum accuracy.
Why Choose Cementl for Cement Manufacturing Equipment?
Cementl is a trusted name in the cement manufacturing industry, known for delivering high-quality, reliable equipment tailored to modern production needs. Here’s why cement plants around the world choose Cementl:
- Innovative Technology:
- Advanced automation systems for enhanced control and monitoring.
- Energy-efficient designs that reduce operational costs.
- Durability and Reliability:
- Machines built from high-grade materials for long-term performance.
- Robust designs to withstand the harsh conditions of cement production.
- Comprehensive Solutions:
- From crushers to kilns and grinding mills, Cementl offers end-to-end solutions.
- Customizable equipment to meet specific production requirements.
- Environmental Commitment:
- Energy-efficient machinery that reduces carbon footprint.
- Solutions for utilizing alternative fuels and recycling industrial waste.
Conclusion
Cement manufacturing requires a variety of specialized machines to ensure efficient, high-quality production. Crushers, coal grinding pulverizer mill systems, rotary kilns, vertical roller mills, and screening machines each play a crucial role in transforming raw materials into finished cement.
By investing in reliable equipment from Cementl, cement manufacturers can enhance operational efficiency, reduce costs, and ensure consistent product quality. Whether you’re upgrading existing machinery or building a new plant, Cementl‘s expertise and innovative solutions provide a solid foundation for success in the competitive cement industry.