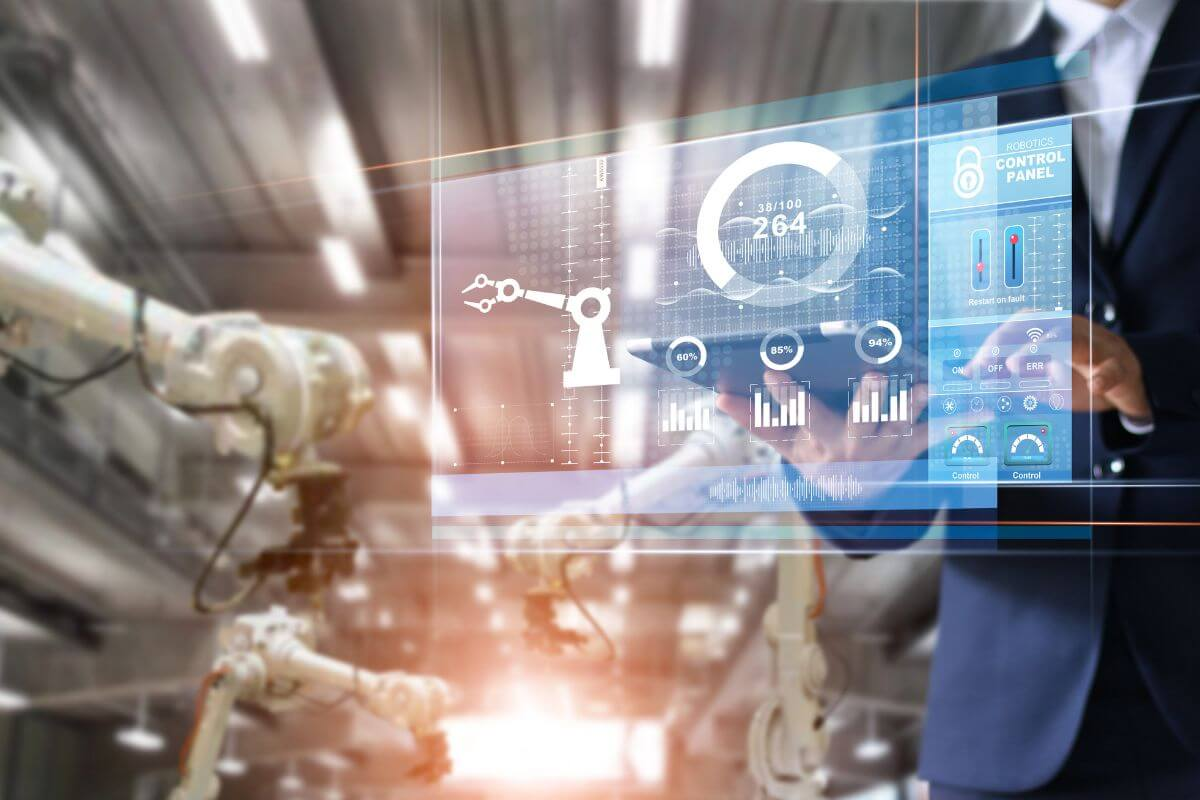
Factory Automation: A Step-by-Step Guide to Digitizing Your Factory in 2023
- 0
Welcome to the future of manufacturing, where automation is transforming factories into hubs of innovation. In this guide, we’ll navigate the steps to digitize your factory in 2023. Embracing factory automation streamlines processes, boosts productivity, and enhances profitability, marking a shift from manual labor to cutting-edge technology. So, let’s explore the benefits and steps toward taking your factory into the digital age for increased efficiency and competitiveness.
Why Digitize Your Factory?
In today’s competitive business landscape, staying ahead is important, especially in manufacturing, where digitizing the factory brings significant benefits. Factory automation replaces manual labor, enhancing productivity and efficiency while reducing errors and costs. Digitization enables real-time data collection and analysis, empowering data-driven decision-making and process optimization.
Automation improves workplace safety by assigning hazardous tasks to robots and protecting employees from potential injuries. Beyond productivity gains, automating repetitive tasks frees up human resources for innovative work, fostering creativity and boosting morale. Digitizing offers evident advantages: heightened productivity, improved decision-making, enhanced workplace safety, and unlocking workforce potential. Now, let’s delve into the step-by-step process of achieving this transformative journey!
Types of Automation Processes
Step 1: Assess Your Current Manufacturing Processes
The first step in digitizing your factory involves a detailed assessment of current manufacturing processes. This evaluation examines raw material intake, inventory management, production lines, and quality control, identifying areas for improvement and automation. Data on key performance indicators (KPIs) such as production output and cycle times guides the prioritization of automation efforts.
Involving cross-functional teams ensures a comprehensive understanding of challenges and opportunities. The assessment aims to provide clarity on areas for enhancement rather than fault-finding. With this thorough assessment, the next step in digitizing your factory involves identifying specific areas for automation, as detailed in an upcoming blog post.
Step 2: Identify Areas for Automation
After assessing current manufacturing processes, the key to successful automation lies in identifying specific areas within the factory that can benefit from it. This involves a detailed analysis to pinpoint repetitive, time-consuming, or error-prone tasks. Focus on the production line to address bottlenecks and inefficiencies, considering automation for manual tasks like product assembly.
Evaluate inventory management for potential stock issues and implement automated tracking solutions. Quality control can be enhanced with machine vision systems to detect defects swiftly and accurately. Additionally, explore automation opportunities in maintenance and asset management to optimize routine inspections and repairs.
By scrutinizing each operational aspect, businesses can leverage automation to enhance efficiency, productivity, and cost savings, positioning themselves for success in the digital era.
Step 3: Choose the Right Automation Technology
After identifying areas for automation, the important next step is choosing the right technology. Research solutions aligned with your needs, considering factors like cost, scalability, and compatibility. Consult industry experts, involve key stakeholders, and engage with vendors for insights on performance and reliability.
Narrow down options, conduct thorough testing, and pilot programs for seamless integration. Stress that the choice isn’t one-size-fits-all; tailor it to your unique business needs, focusing on long-term sustainability and growth. Careful selection establishes a foundation for streamlined operations, increased productivity, reduced errors, and improved quality control, ultimately leading to enhanced profitability and customer satisfaction.
Step 4: Implement and Test Automation Systems
In Step 4 of the automation process, start by creating a detailed implementation plan outlining system installation and integration. Ensure the availability of necessary hardware and software before proceeding. Rigorous testing, including simulations and trial runs, follows setup to assess system performance.
Promptly address any issues or glitches discovered during testing to optimize efficiency. Close collaboration between team members and automation experts is important, with regular communication to ensure smooth implementation and minimize disruptions in production schedules. Implementing automation systems requires careful attention to detail and thorough troubleshooting. Patience is key as unexpected challenges may arise.
By diligently following through with Step 4, effective integration of automation into factory operations can be achieved, minimizing downtime and maximizing productivity. The next step is Step 5: Training Employees on New Processes!
Step 5: Train Employees on New Processes
Proper employee training is essential for successful factory digitization. Despite the efficiency of automation, its effectiveness relies on well-trained personnel. Conduct comprehensive training sessions, provide clear instructions and hands-on experience, and encourage questions.
Consider assigning dedicated trainers for ongoing support, recognizing varying technological proficiency levels. Tailor training for different needs, fostering a culture of continuous learning. By investing in comprehensive training, you empower your workforce to adapt seamlessly to automated processes, ensuring a smooth implementation and maximizing productivity gains from factory automation technologies.
Benefits of Factory Automation
Factory automation brings several benefits to manufacturing:
Increased Efficiency: Automation streamlines operations, reducing human error and boosting production speed, resulting in higher output.
Improved Quality Control: Precise automation ensures consistent product quality, minimizing variations and defects. Automated inspections promptly identify deviations for adjustments.
Enhanced Safety: Automation reduces the need for manual labor in hazardous tasks, protecting workers from potential injuries.
Cost Savings: Despite initial costs, automation leads to long-term savings by eliminating manual labor, reducing material waste, minimizing downtime, and optimizing energy usage.
Flexibility and Scalability: Automation provides flexibility to adapt to changes in production demands or product variations efficiently.
Competitive Advantage: Companies embracing automation stay ahead by delivering products efficiently while maintaining high quality, gaining a competitive edge.
Innovation Potential: Automation opens opportunities for innovation, allowing the integration of advanced technologies like artificial intelligence, machine learning, and data analytics for further optimization.
Challenges and Potential Solutions
Implementing factory automation is a transformative step that brings significant advantages, but being mindful of the challenges is important for a successful transition. Here’s a recap and some additional insights:
Initial Investment:
Challenge: Upgrading machinery, implementing new software, and training employees require a substantial initial investment.
Solutions: Recognize the long-term cost savings and efficiency gains. Plan and prioritize investments strategically to maximize returns.
Employee Resistance:
Challenge: Employees may resist automation due to fears of job loss or discomfort with new technologies.
Solutions: Transparent communication about the benefits, clear training programs, and fostering a culture of continuous learning can address these concerns.
Integration Issues:
Challenge: Ensuring compatibility and seamless integration between different automation systems.
Solutions: A careful selection of technologies with robust integration capabilities and ongoing monitoring can prevent integration challenges.
Cybersecurity Threats:
Challenge: The increase in connected devices introduces cybersecurity risks.
Solutions: Implementing strong cybersecurity measures, including firewalls, encryption, regular updates, and employee education, is important to safeguard against potential threats.
Maintaining Flexibility:
Challenge: Automated systems may face challenges in adapting to changing production needs.
Solutions: Design systems with flexibility in mind, allowing for easy adjustments and reconfigurations as production requirements evolve.
Continuous Learning:
Challenge: In a rapidly evolving landscape, keeping up with technological advancements is essential.
Solutions: Invest in ongoing training programs for both management and employees to stay abreast of the latest developments in factory automation.
Future of Factory Automation
The future of factory automation is poised for significant transformations with the integration of cutting-edge technologies. Let’s dive deeper into the key aspects:
Increased Connectivity and Integration:
Future Outlook: Embracing Industry 4.0 principles, factories will witness enhanced connectivity through technologies like IoT and AI. This interconnectedness will enable real-time data analysis, predictive maintenance, and more informed decision-making.
Evolution of Robotics:
Future Outlook: Robotics will continue to evolve, playing a more substantial role in manufacturing. Advanced and versatile robots will be deployed across assembly lines and material handling tasks, contributing to increased precision and speed in repetitive processes.
Machine Learning Advancements:
Future Outlook: Advancements in machine learning algorithms will empower machines to learn and adapt from their experiences. This continual performance improvement will make automated systems more intelligent and flexible, capable of responding to changing conditions and demands.
Virtual Reality (VR) and Augmented Reality (AR):
Future Outlook: VR and AR technologies will revolutionize training programs within factories. Providing immersive simulations and overlays on physical equipment, these technologies will facilitate more effective skill acquisition for workers, reducing risks associated with hands-on training.
Addressing Job Displacement Concerns:
Future Outlook: The transition to increased automation will raise concerns about job displacement. To address this, proactive measures such as reskilling programs and the creation of new roles centered around managing automated systems will become essential.
Conclusion
In conclusion, factory automation is indispensable in the dynamic manufacturing landscape, driving enhanced productivity, efficiency, and competitiveness. This guide underscored important steps in the digitization journey, emphasizing the assessment, selection, and implementation of automation technologies. Prioritizing employee training ensures a seamless transition and unlocks the full benefits of automation.
Despite challenges, the advantages—increased productivity, cost efficiency, improved product quality, and adaptability to market dynamics—reinforce the strategic importance of automation. Successful adoption necessitates strategic planning that addresses both technical complexities and human considerations. Looking forward, the future of factory automation holds promise with advanced technologies, such as collaborative robots, AI, and machine learning, heralding continuous innovation and transformation in manufacturing processes.